冷間鍛造とは、加熱していない常温の金属材料を金型で成型する加工方法です。 金属の塑性を活かして加工することから、「塑性加工」とも呼ばれています。通常の抜き・曲げのプレス加工では成形できない形状が生産可能なため、切削部品のプレス加工化や、複数部品の一体化などへ応用することで、コストダウンに繋がる工法転換が可能となります。
冷間鍛造(板鍛造)とは
冷間鍛造は“塑性加工”のひとつであり、常温下で金属に圧力を加えることで変形させ、必要な形状に成形する加工法です。
塑性加工とは?
材料に力を加えて変形させ、力を取り去った後もその形が残る性質のことをいいます。対義語は“弾性”で、変形させてもバネのように戻る性質のことを言います。
当社の冷間鍛造は、板材(コイル)を順送りしながら、常温状態で金型を用いて鍛造加工する工法であり、冷間鍛造の中でも『板鍛造』と呼ばれるプレス工法になります。
「冷間鍛造」に対して、材料の再結晶温度以上(約1000〜1200℃)になるまで加熱してから加工する「熱間鍛造」、そして中間の温度である(約300〜850℃)に加熱して加工する「温間鍛造」が存在します。
板鍛造プレスも含めて、ヘッダー加工やパーツフォーマーなどの加工法も、すべて冷間鍛造に分類され、パンチとダイを用いて加工する点では『型鍛造』とも呼ばれます。
難易度の高い形状では、鍛造加工後に焼鈍工程を入れることで素材硬度を下げ、複数回の鍛造加工で徐々に形状をつくる工法もあり、同じ冷間鍛造という呼び名でも区別する必要があります。工法によって得意な加工形状もそれぞれ違いますので注意が必要です。
冷間鍛造のメリット
冷間鍛造には、以下の3つのメリットがあります。
通常のプレスでは困難な形状が加工できる
通常プレスの抜き曲げでは、加工できる形状は限られてしまいますが、冷間鍛造の技術を取り入れることで、部品の厚みを変えたり、皿モミやザグリなどの形状を加工する事が可能です。
加工スピードが速い
冷間鍛造は切削加工にくらべて加工スピードが速く、形状にもよりますが毎分50個程度の生産が可能です。プレス工程のみで、 ネットシェイプ(部品の最終形状)・ニアネットシェイプ(2次加工で最終形状となる半製品のこと)の状態まで加工できるため、 リードタイム短縮にもつながります。
強度の高い製品が加工できる
金属にはファイバーフロー(鍛流線)というものがあります。金属は結晶組織によって構成されており、この金属組織のもつ流れを”ファイバーフロー”といいます。このファイバーフローは、金属の強度を決定する重要な要素の一つです。切削加工ではこのファイバーフローが切断されてしまいますが、冷間鍛造によるプレス加工では、このファイバーフローが保たれたまま成形されるため、衝撃に強く、疲労強度に優れた製品が仕上がります。
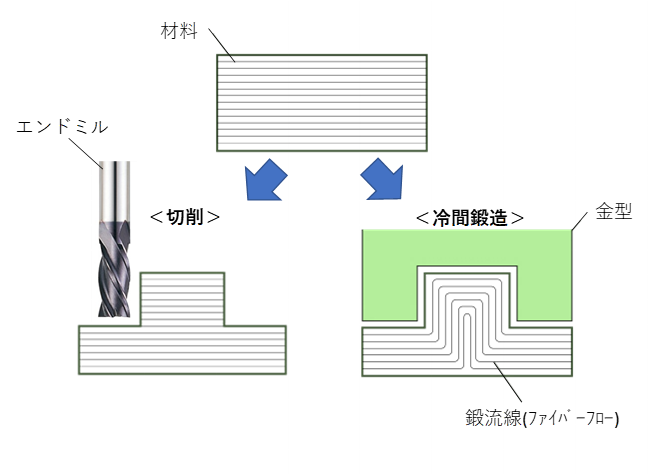
冷間鍛造への工法転換でコストダウン
今まで切削加工で製作されていた製品や複数部品の一体化など、冷間鍛造の技術を用いてプレス加工への工法転換することでコストダウンが可能です。なぜ、そのようなコストダウンが可能なのをご説明いたします。
切削部品の冷間鍛造加工への工法転換
切削で生産されていた部品をプレスで生産することで加工工程を合理化することに繋がります。
プレスによる冷間鍛造では、切削にくらべて加工スピードが速く、加工コストを大幅に削減することができます。2次切削で加工していたザグリや皿モミなどの形状も、冷間鍛造で加工できれば2次切削のレス化にもつながり、コスト削減の効果も大きくなります。
冷間鍛造による複数部品の一体化加工
複数の部品を溶接したり、カシメで接合していた製品を、冷間鍛造加工により一体化成形することでコストダウンが可能です。
冷間鍛造加工のみで製品を完成させることができると、従来おこなっていた溶接・カシメ作業は不要となり、2次加工費が発生しないため、大幅なコストダウン・リードタイム短縮につながります。複数部品を接合していた場合と比較し、冷間鍛造での加工品は接合部分が無いため、製品強度・耐久性が高くなることもメリットとして挙げられます。
冷間鍛造加工への工法転換の注意点
切削加工から冷間鍛造への工法転換、冷間鍛造による複数部品の一体化は、メリットだけではありません。工法転換に向かない形状や、注意点についてお伝えいたします。
小ロット品には向いていない
冷間鍛造加工を行うには専用の金型が必要です。製品単価とは別に金型費用(イニシャル)が発生し、この金型は高額なことから、イニシャルの償却を含めてメリットを出せるかがポイントとなります。小ロット品ではトータルコストに占めるイニシャルの割合が高いため、リードタイムの短縮には繋がっても、コストダウンとはならない場合もあり得ます。
部品形状によりますので正確な数字ではありませんが、ロット5万個程度の切削部品をプレス加工化することで、30〜50%程度のコストダウンが期待できます。
材料歩留まりは悪くなる可能性がある
板材(コイル)からの加工しかできないため、加工物のサイズ・形状は制限を受けます。製品形状によってはスクラップとして捨てられる部分が多くなってしまい歩留まりが悪くなります。極端な例では材料歩留まりが30%以下のプレス製品も存在します。
冷間鍛造への工法転換によるコストダウン事例
切削からプレス加工への工法転換で40%コストダウン
冷間鍛造の技術を活用したピックアップ加工事例
冷間鍛造技術を活用した当社のピックアップ加工事例を下記にてご紹介します。
皿加工厚板一般部品
こちらは、自動車のドア用フックストライカです。材質はハイテン材(SPH310)、板厚は6.0tで、順送プレス加工にて生産しております。
皿モミ形状が特徴的ですが、潰して形状を作る際に穴の形状が歪んでしまい、真円にならない課題がございました。当社では、皿モミ形状を加工した後に、もう一度穴を仕上げる工程を追加することでこの問題をクリアしました。
ギヤ歯冷間鍛造複合機能部品
こちらのギヤは、内歯と外歯があるレバーギヤで、現行品は焼き入れで硬度を確保しているとのことでした。後継タイプとして焼き入れ無しを検討されていましたが、590級ハイテンで製品加工するにあたり、せん断量の確保やツブシ形状の成形ができるかが課題でした。
当社では、いままでに培ってきた冷間鍛造と精密せん断のノウハウを生かし、2つの技術を複合加工できる順送金型を設計し、無事に量産ラインの立ち上げにつなげることができました。
冷間鍛造段付き穴位置難加工部品
こちらのプレス部品は、元々は切削加工で製作される予定の部品でしたが、プレス化できないかとのことで当社にご依頼いただきました。社内で検討したところ、肉厚が材料板厚よりも薄くなる箇所があり、冷間鍛造加工するための工程数と、設備加工能力が課題となりました。
様々なアプローチから方法を検討した結果、冷間鍛造順送金型で加工することをご提案し、無事に量産化することに成功し、当初予定していた切削加工と比べ約40%のコストダウンを実現しました。
S字曲げ皿加工ダレ無し部品
こちらの部品は、中央部がS字に段曲げ加工がされており、また両端の円形状部分の抜きダレを極小で抑え、0.15の平面度を確保。さらに穴部分にC面加工が必要という金型ステージが多工程となる部品でした。
そこで当社では、精密せん断加工の技術を応用し、さらに段曲げ加工とC面加工を考慮した工程レイアウトを工夫することで、量産化を実現いたしました。
銅冷間鍛造 ヒートシンク部品
こちらのヒートシンク部品は、製品の厚さを増肉で実現し、なおかつ各寸法は高精度という部品でした。入手可能な材料板厚から増肉加工で形状を出し、寸法公差を実現できるかが課題でした。
当社では、金型刃物の精度と強度を両立させ、増肉加工での厚み確保できるかがポイントでしたが、トライ&エラーを重ね、最適な条件を掴むことで量産化に成功しました。
当社の冷間鍛造加工事例
冷間鍛造のことなら、工法転換プレス加工技術.comまで!
いかがでしたでしょうか。今回は冷間鍛造のメリット・デメリットについてご紹介しました。
工法転換プレス加工技術.comを運営する熊谷精機株式会社は、プレス加工のプロフェッショナルとして、主に自動車、産業機械に向けてあらゆる部品を製作してまいりました。
当社は、様々な工法転換のご提案実績がございます。切削部品のプレス化や複数部品の一体化、FB(ファインブランキング)製品の一般プレス加工化など、当社がこれまで培ってきた精密せん断加工技術、冷間鍛造加工技術を用いて、お客様のご要望の製品を製作いたします。
さらに、当社では月産100〜100万個以上まで様々な数量に対応することができます。工法転換を検討する際は、ご要望に応じて生産性検証を行い、あらゆる課題を抽出した上で合理化提案をいたします。
プレス加工に関するお悩みをお持ちの方は、工法転換プレス加工技術.comまでお問い合わせください!